Six ways to implement construction cost control
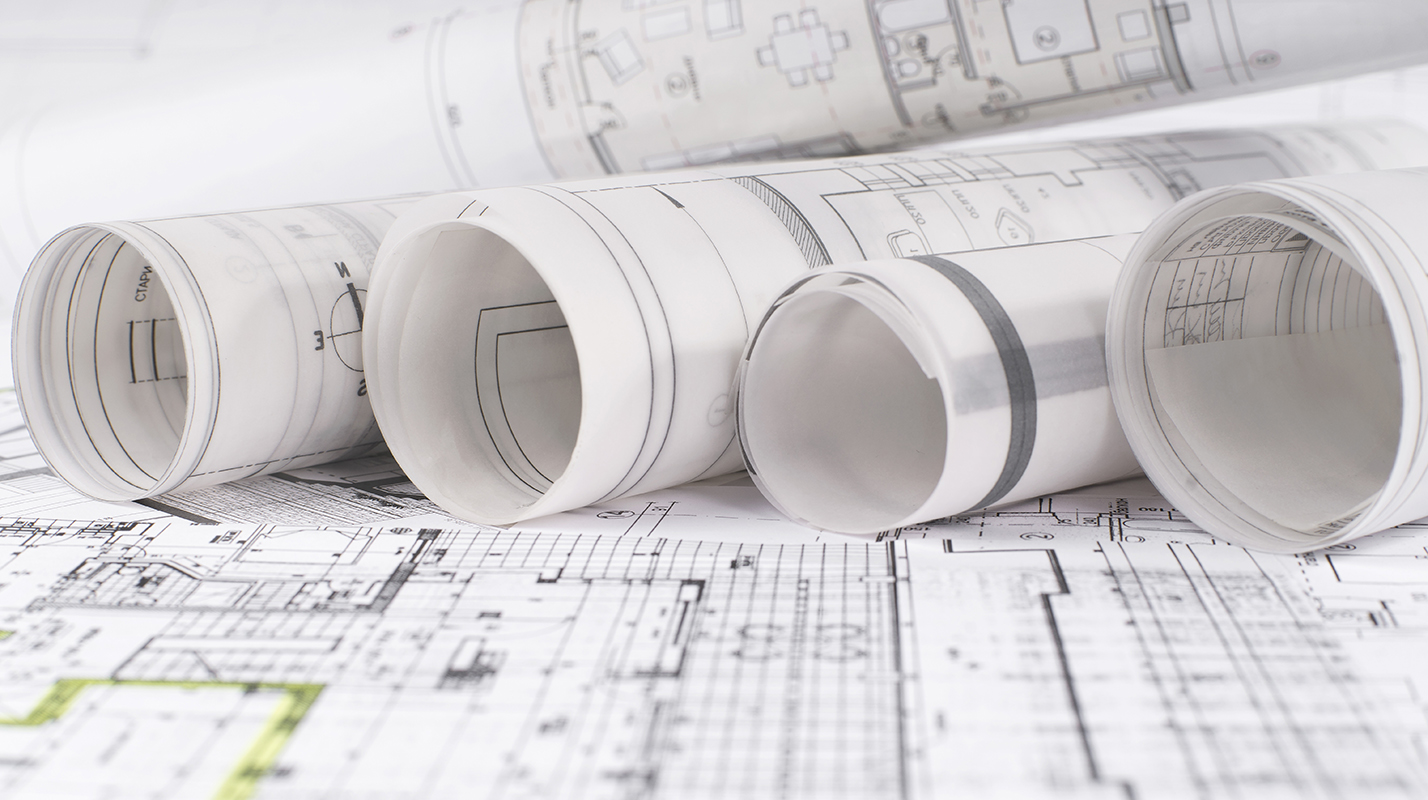
How to plan for better cost control outcomes on your project
From labor rates to equipment prices and indirect costs, there are myriad factors affecting construction budgets. And while your estimation might appear accurate at first, it’s crucial to understand cost control options so that you can respond to the unexpected and stay on budget.
To learn more, we caught up with Joe Stramberg, a principal in Treanor’s Higher Education studio. Here, he shares cost control measures when trying to implement great design while staying within your means. Following are six paths to cost control—without compromising the integrity of your vision.
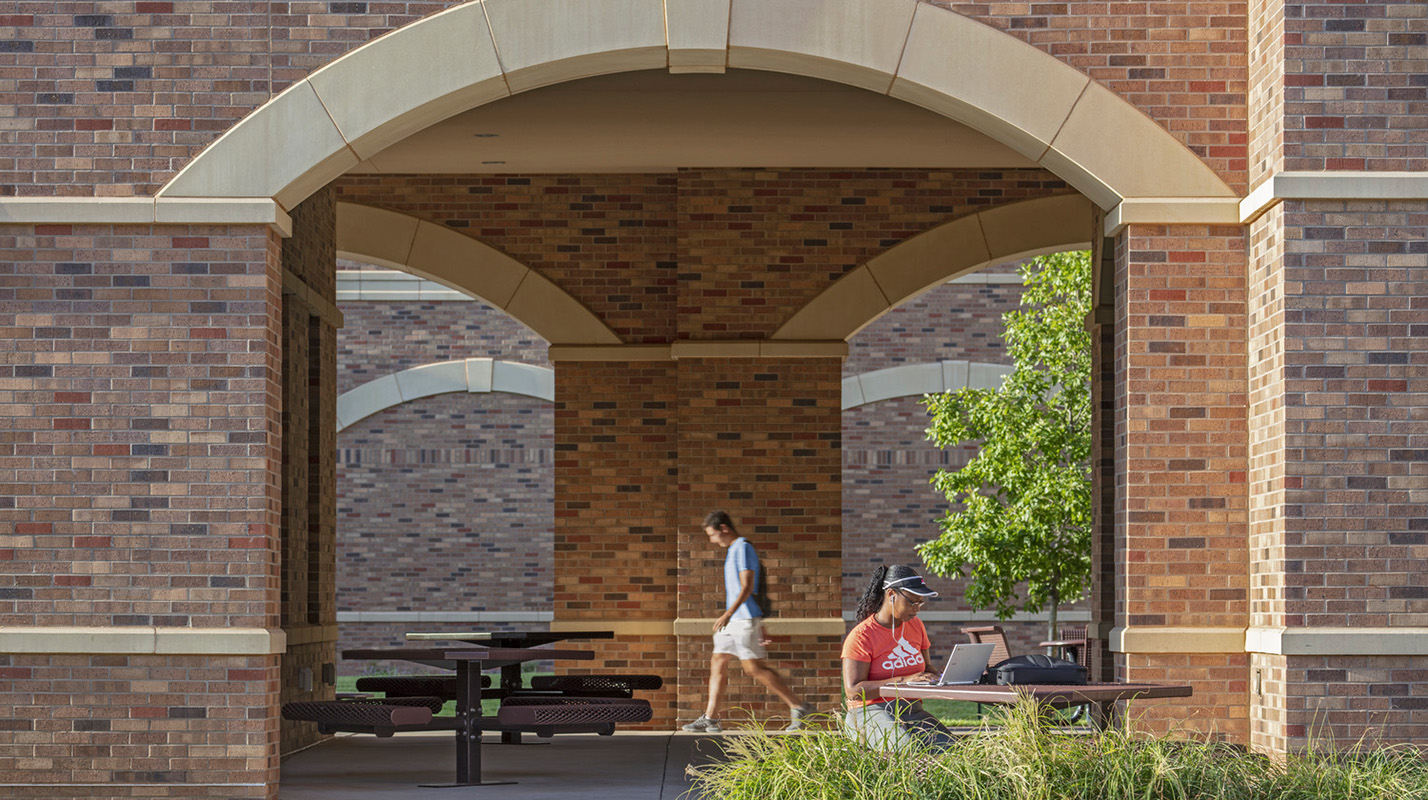
1. Starting early—and together
Dive in as deep as possible early during the program phase, thinking about not only dollars per square foot, but also detail costs of structural and mechanical systems. Try to begin to define costs of those projects even before pencil hits the paper and develop a cost model right from the beginning, right from the programming efforts.
“It’s very critical,” Joe says. “Make sure you are planning for budget contingencies and really have conversations about the risks of the project from a cost standpoint, whether that’s a tight schedule or a complex renovation project with multiple phases.”
Having conversations early and getting a contractor’s perspective on risks early on is also important. Joe recommends approaching it with eyes wide open before arriving at the design process to develop strategies that will mitigate risks. “It’s a collaborative effort,” says Joe. “Be as proactive as you possibly can in having that conversation.”
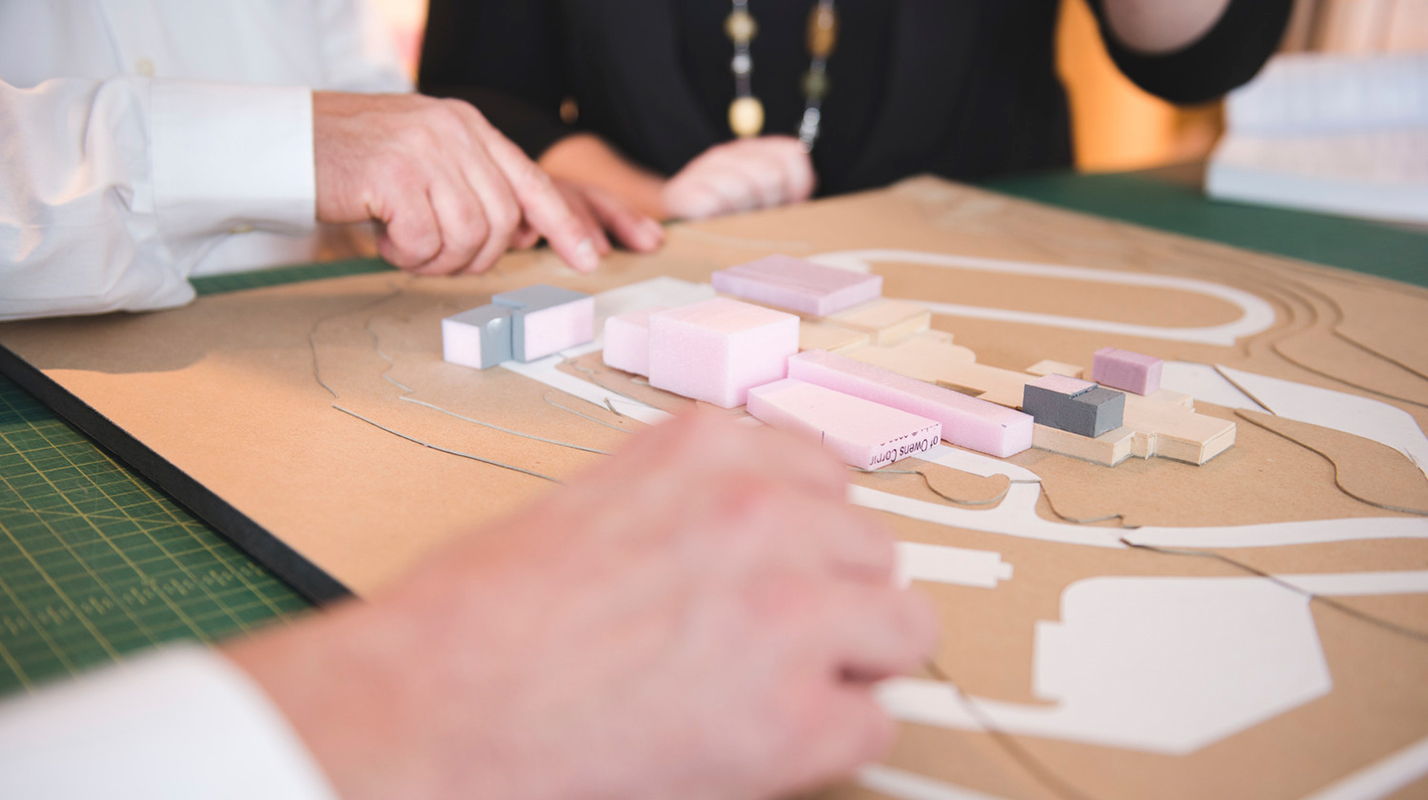
2. Developing budget-protecting alternatives
Another way to implement cost control is by taking a more proactive approach and establishing targets. Plan your base bid to 90% of the budget, then develop clear and concise add alternates up to 105% of budget.
If materials increase because of the market at the time of the bid, you now have a project that’s awardable. “If conditions are favorable, you may be able to upgrade, but by planning for alternatives, this strategy frames the level of expectation,” says Joe.
3. Using your knowledge base
An experienced team by your side who understands your project type and its specific market will also help you avoid common pitfalls and control costs. “Bringing that historical knowledge base and knowing what things cost is crucial,” says Joe. And a diverse team only makes this stronger.
A cost consultant will bring a broad, national perspective outside of the team, in addition to the construction manager and pre-construction teams, and of course, your architect. “As part of the project team, they bring multiple perspectives and views,” says Joe.
A client who clearly understands the needs and scope of the project helps even more, not to mention the institutional knowledge brought to the table.
“Having a vigorous and thorough reconciliation review process of an independent estimate allows us to identify any gaps in scope or overlaps.”
Joe Stramberg, Principal, Treanor
4. Contingency planning
Particularly now, project teams must consider adding contingency line items for tariffs. While you should plan for a normal escalation of commodity pricing, we’re facing an even greater anticipated increase above and beyond with steel and aluminum tariffs on the rise. While it would be impractical to plan for every disaster scenario, adding some buffer in the budget will benefit you in the long run.
5. Designing shell space
Another method to control costs: designing shell space, which you can build and add programming to later. “You may not be able to build out everything today, but the layout and design will be ready for the future,” Joe says. “It’s wise to build the vision on day one but have a plan in place so that when funds do become available, you can see it through.”
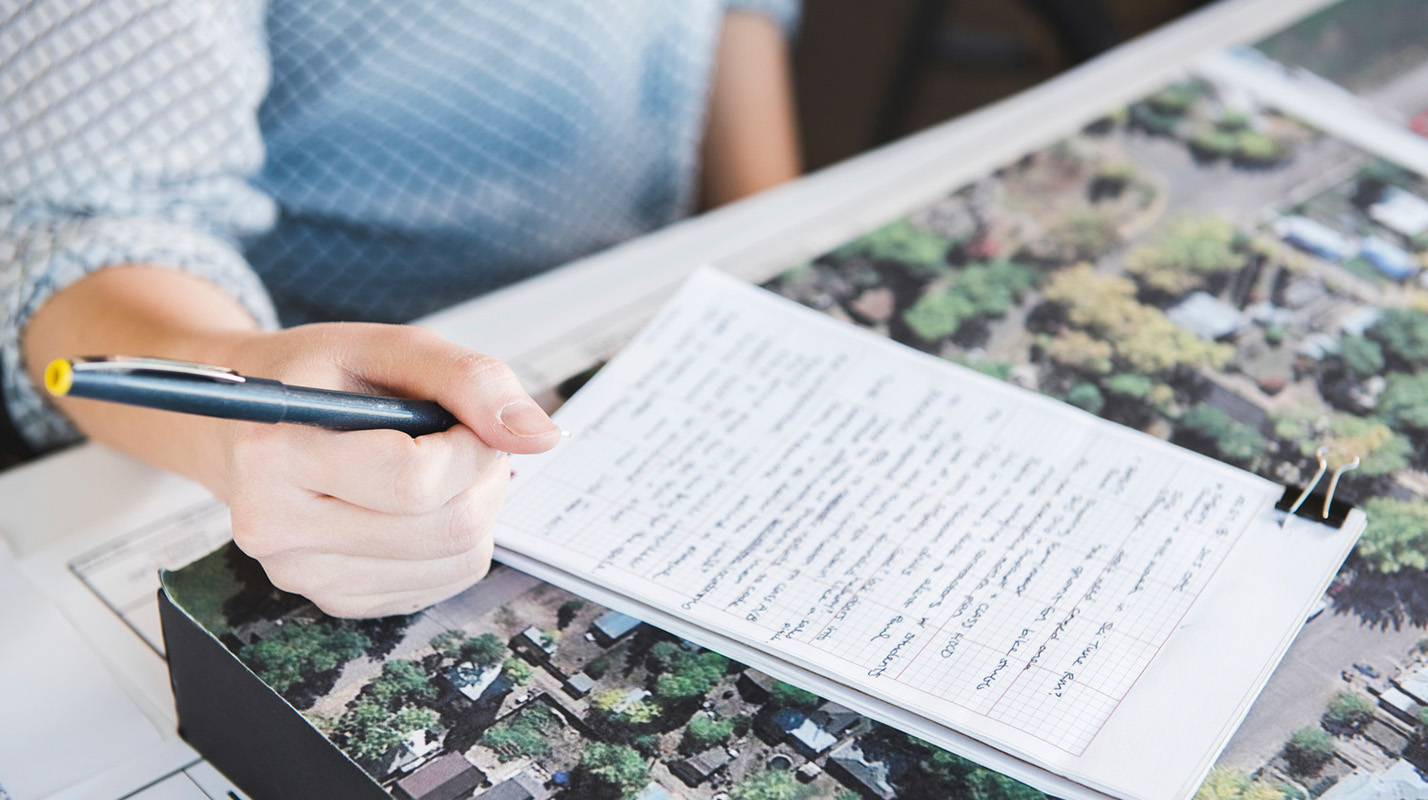
6. Getting creative with resources
A final option to consider is redistributing resources. For example, by thinking outside the lot, prefabrication can save you time and money, since construction can be done simultaneously while the land is being prepared.
Another way to reallocate resources in a way that cuts costs is considering a more economical—yet still durable—structural system and placing dollars strategically where students see them most. “If there is limited amenity space, put your dollars there,” says Joe.
“Support what benefits the most number of students—furniture, technology, amount of amenity space, access to natural daylight. You want to create a home-like space where students want to be.”
Joe Stramberg, Principal, Treanor
There are many ways to implement cost control, but be wary of value engineering, a last resort. That optimization often eliminates scope or reduces quality. Instead, by working as a team, planning far in advance, and considering alternative paths, you can ensure your budget will stay on track while designing space that supports—in Joe’s case—the students using the facility.
“I always think about the students outside of class, where they’ll make connections that will last a lifetime,” Joe says. “It’s an opportunity to build community.”
Authors
Stay on the leading edge
Stay up to date on emerging trends, research, hot topics, and more delivered conveniently to your inbox.
"*" indicates required fields