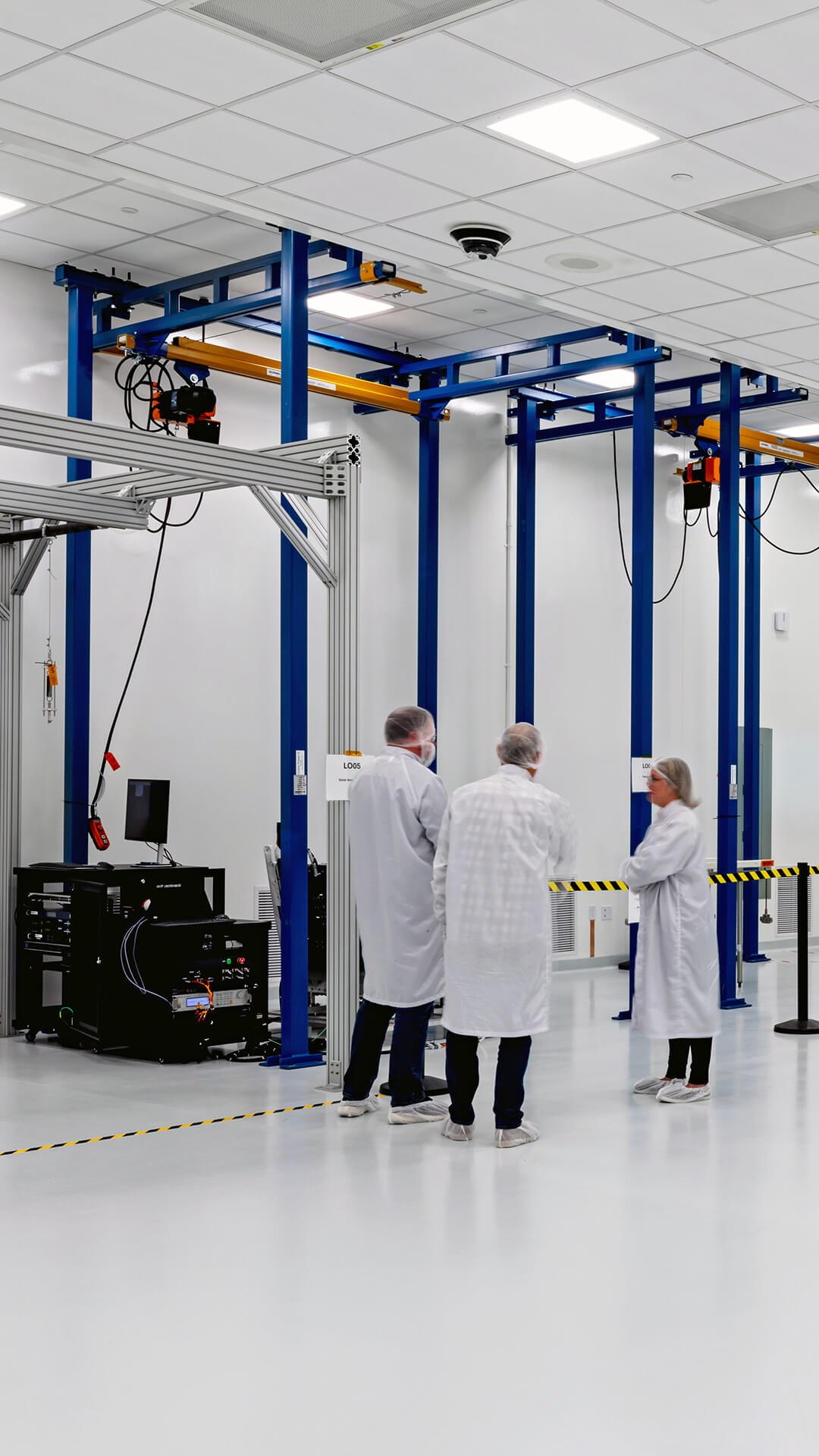
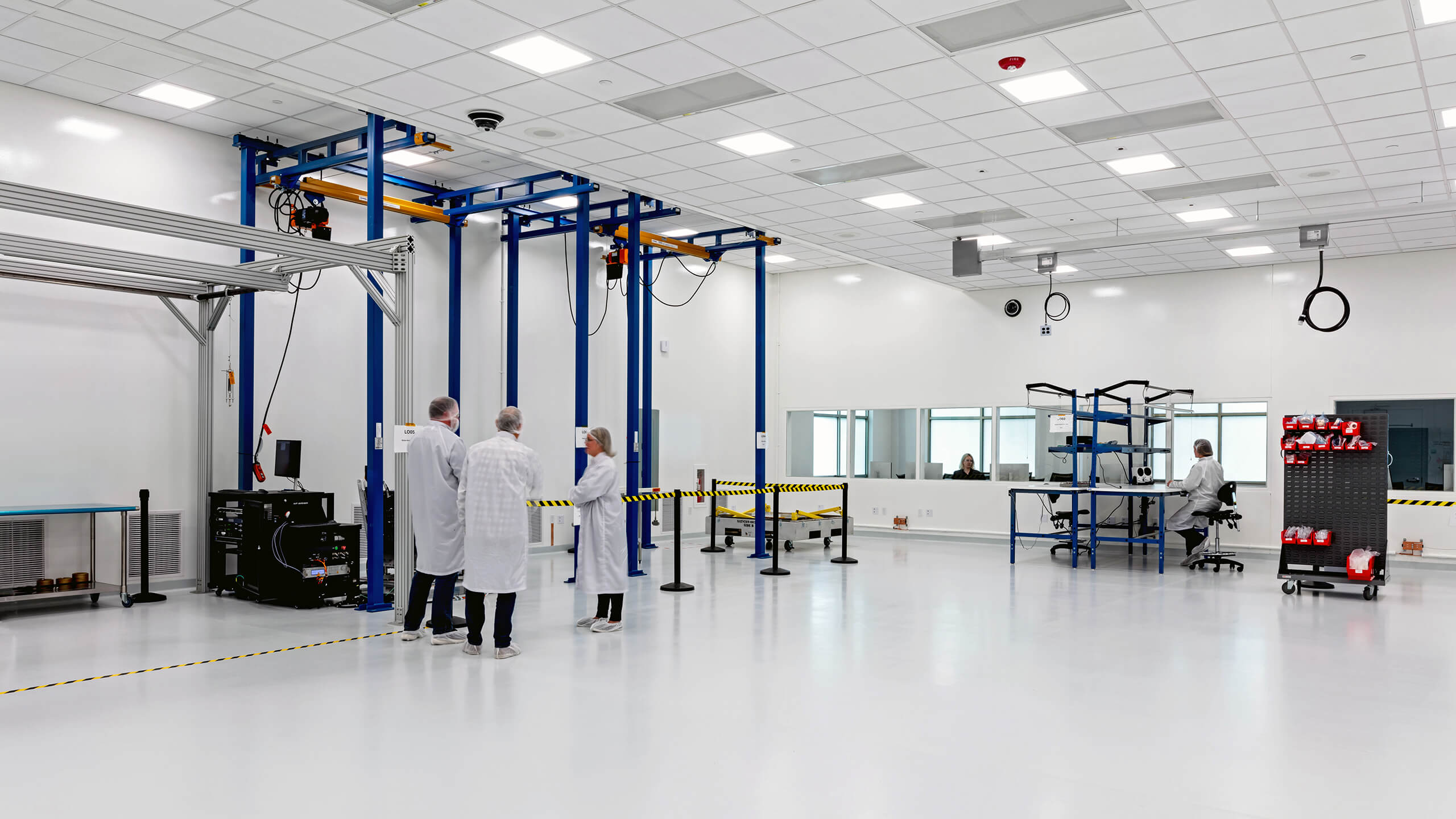
Production Facility & Cleanroom
Trailblazing a path to space
The largest barriers to space exploration and research are speed and simplicity. Our client, Loft Orbital, is a satellite manufacturer and software developer that understands these hurdles are insurmountable for many entities. To reduce these burdens, Loft Orbital created a system that allows multiple entities to leverage the payload of an individual satellite.
Loft builds the space infrastructure that lets any company, government or institution harness the benefits of space.
Loft Orbital
Leveraging advanced manufacturing design specialty to exceed goals
Because of the growing commercial investment in space accessibility, our client has seen increasing productivity demands and growth within their organization. As a specialist within advanced manufacturing and cleanroom facilities, including the precise environments needed for satellite manufacturing, Loft brought our team into the project for a peer review of the existing design and to provide recommendations.
Through multiple stakeholder meetings, it was determined that a redesign of the facility was necessary to better align the facility’s design with the client’s expectations and vision for the future. By working with various user groups, our team developed a concept centered around transparency and flexibility.
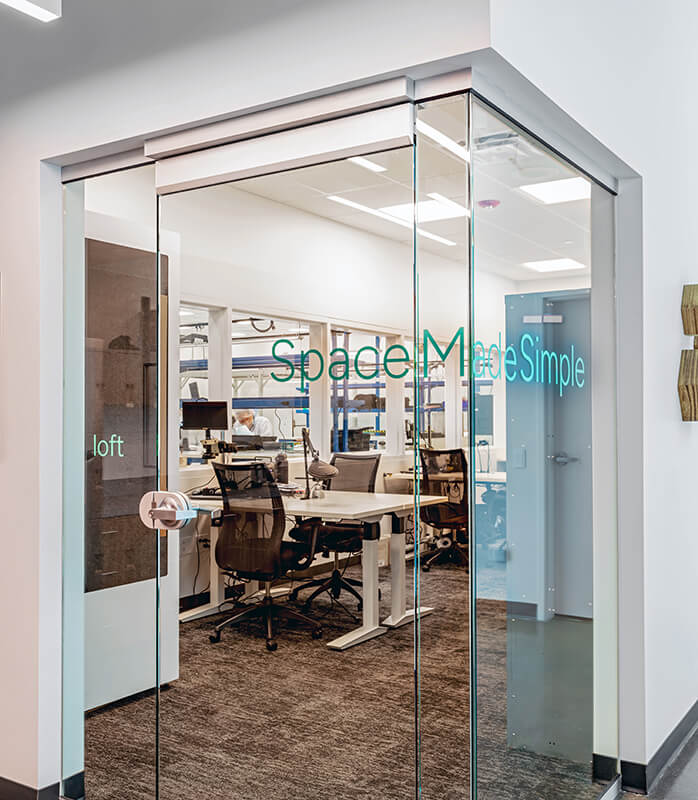
Project goals
- Redesign the facility so each space embodies the client’s mission
- Showcase the work occurring within the cleanrooms
- Address electrical usage
- Provide a building that is functional, delightful, comfortable, and safe for the occupants and visitors
Cleanrooms and collaboration
All within the same space and ISO 8 classification, the cleanrooms are designed to support manufacturing, satellite component integration, environmental testing, and research and development. The new space is designed for flexibility, increasing the efficiency of Loft’s workflow. This allows Loft to meet current needs, provide room for production increases as the client receives more contracts, and reduce the possibility of environmental contamination. The shared space also encourages interaction and collaboration between each of the client’s different departments.
The redesign also included upgrades to the electrical service of the building to accommodate the high demand these technical spaces require.
External to the cleanroom, the facility boasts a mission control room, a customer showcase control room, employee amenity spaces, warehousing, and storage. This renovated facility is not only Loft’s most efficient facility—it also celebrates the diversity of services offered and puts those services on display. Large windows connect various programmatic spaces from the cleanroom to mission control, and from R&D spaces to the integration floor. Employee amenity spaces and offices run the perimeter of the cleanroom with windows into the cleanroom, further highlighting the work happening within.
Customer showcase facility
Consistent with Loft Orbital’s mission to advance access to space and their belief in customer relationships based on transparency, our client uses the 13,000-square-foot renovated facility to serve as a flagship facility for customer service. Loft’s customers have access to their own control room, allowing access to see real-time integration and deployment of their products. By increasing visibility and accessibility through this facility, Loft Orbital has positioned themselves to lead, innovate, and advance the satellite manufacturing industry.